Break
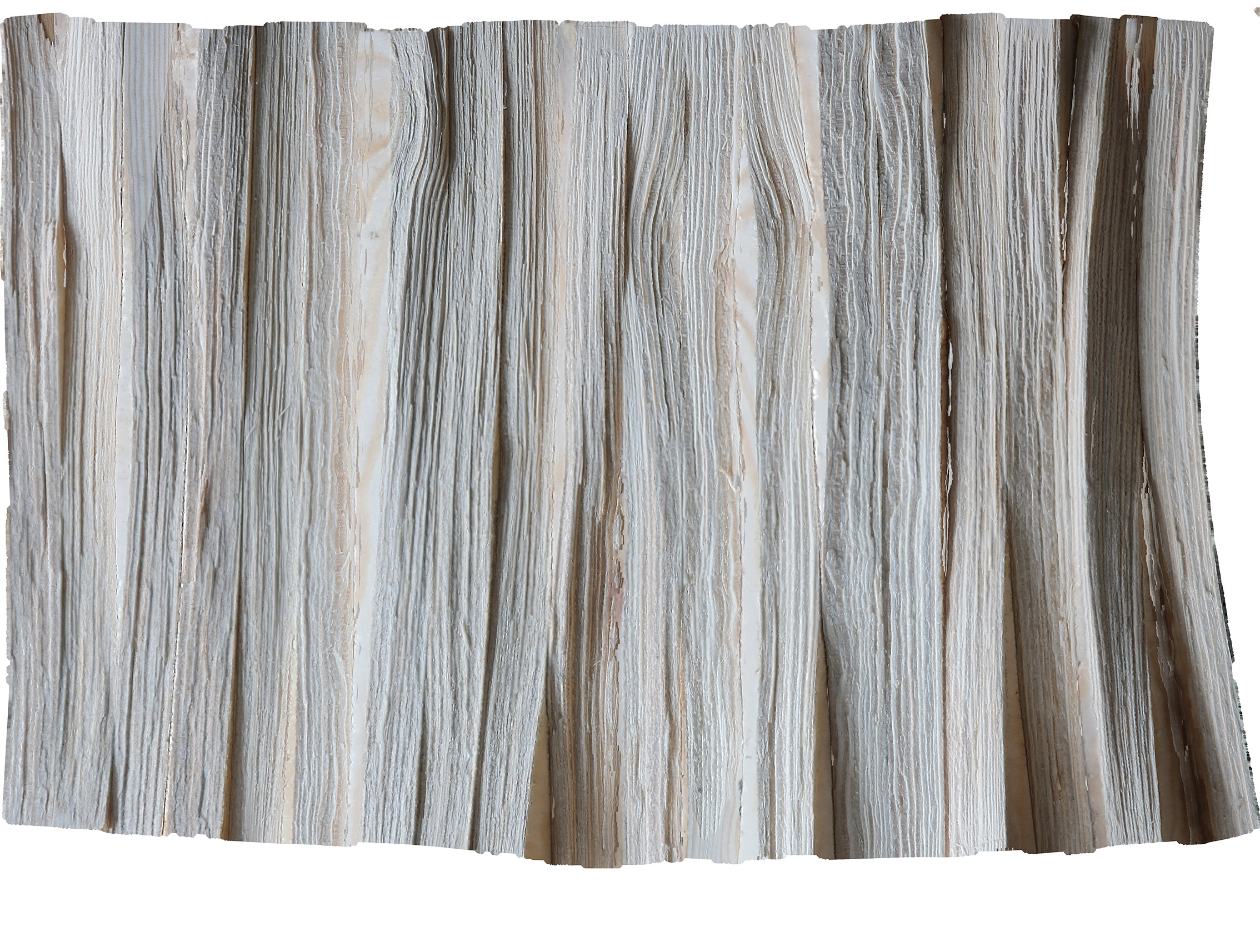
photogrammetry
Photogrammetry uses computer algorithms to create three dimensional (3D) meshes through point triangulation. By inputting many photos of a stationary object, the software analysis each pixel and finds patterns that can help determine a specific points location in 3D space. This creates a mesh that then has color image applied through texturing. All the photos are merged onto a projected view of the mesh from all the determined camera views. This combined image is applied to the mesh to give a color rendition of the object studied. Many details must be taken into consideration while taking the initial photos. Taking good, clear photos with an even light helps by giving a higher fidelity and thus more data for the computer to calculate the points of the mesh. Photos should show the object from all sides as otherwise glitches or holes can appear where the computation could not create meaningful data for that space. The method this thesis utilizes is having the chosen model on a flat table, and walking around taking photos every half step. Making sure to not stand as to cast a shadow over the object. It is a slow and tedious practice but this is necessary to produce a result that can be used in this thesis’s scope. Once this is completed several close up photos where taken to try to increase the resolution of the final image textured onto the mesh.
Photogrammetry uses computer algorithms to create three dimensional (3D) meshes through point triangulation. By inputting many photos of a stationary object, the software analysis each pixel and finds patterns that can help determine a specific points location in 3D space. This creates a mesh that then has color image applied through texturing. All the photos are merged onto a projected view of the mesh from all the determined camera views. This combined image is applied to the mesh to give a color rendition of the object studied. Many details must be taken into consideration while taking the initial photos. Taking good, clear photos with an even light helps by giving a higher fidelity and thus more data for the computer to calculate the points of the mesh. Photos should show the object from all sides as otherwise glitches or holes can appear where the computation could not create meaningful data for that space. The method this thesis utilizes is having the chosen model on a flat table, and walking around taking photos every half step. Making sure to not stand as to cast a shadow over the object. It is a slow and tedious practice but this is necessary to produce a result that can be used in this thesis’s scope. Once this is completed several close up photos where taken to try to increase the resolution of the final image textured onto the mesh.
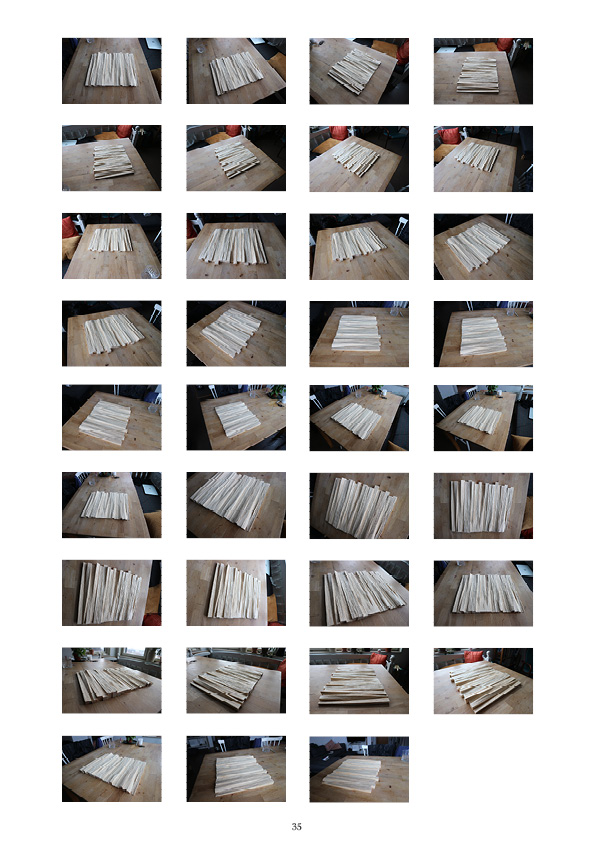

digital to physical
After the generation of a digital model of the second sketch model, a section of the structure was chosen to create a physical model. The front part of the structure was selected because it showed a large variance of textures, different angles between adjacent pieces, and an interesting structural form. The facing direction of each piece became a challenge to handle. The piece had to be designed as a whole, looking at the cleaving characteristics and physical properties of the material it creates. Each piece was arranged digitally to decide how and in which order the fabrication processes would be conducted. The slope of the side angles had to be taken into consideration as the subtractive manufacturing method only works in a vertical direction. This is to say it cannot cut under any material. Plates with sides that had different angles would be solved by having two operations. One to cut the angles facing up. Then the whole workpiece is flipped and the other angles are milled. The tool path generated is a fairly simple ramp. This means that the endmill is always cutting the desired depth of cut. The tool follows a continuous contour around the plate. In this case a 1mm cut was chosen as this increased the fidelity of the angled sides as they are a slope approximation of many steps.
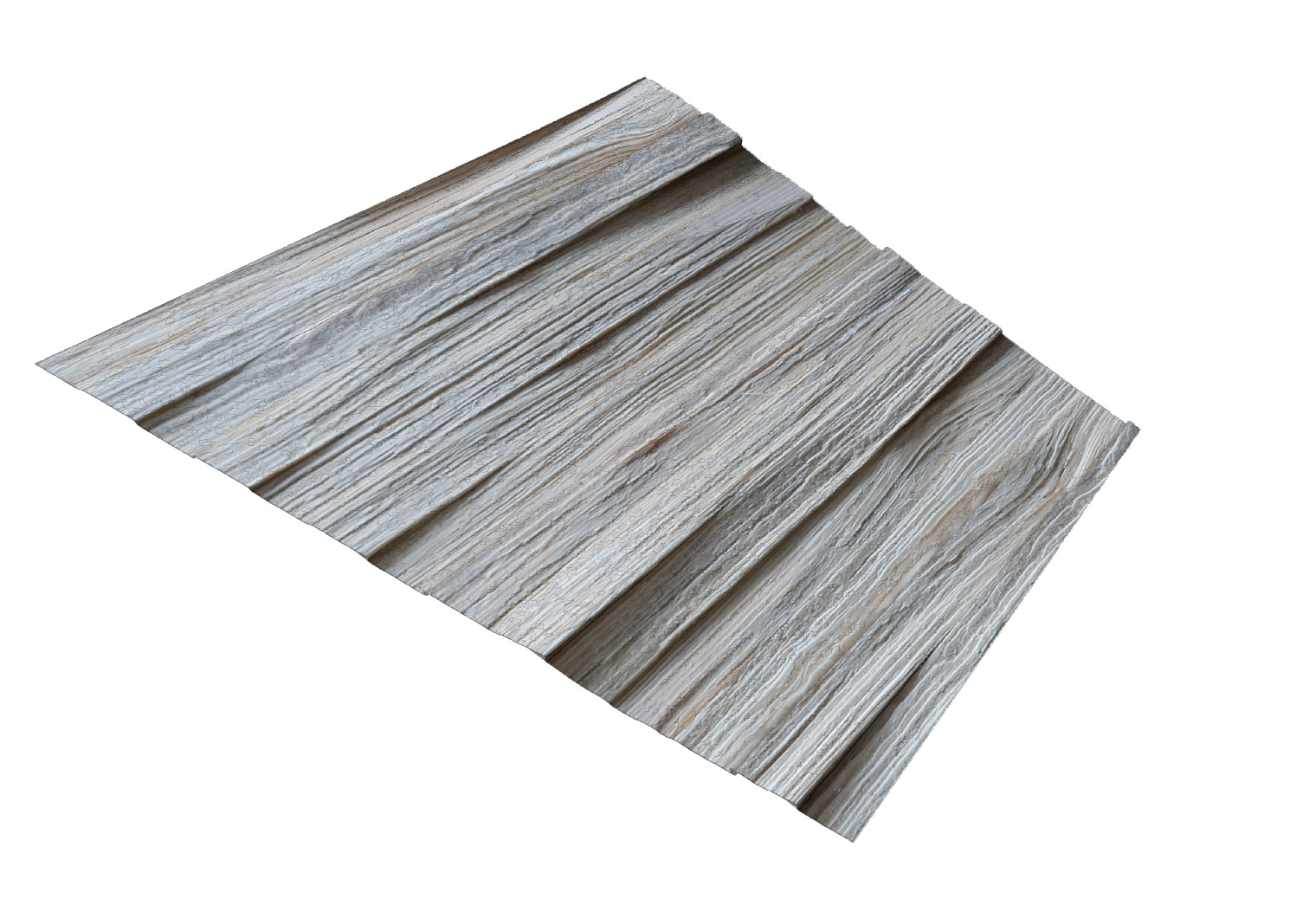
retopologize
Why “fake” a texture? The information is all there. By using a mesh to generate 2d data, we are truncating the data generated during the photogrammetry process. Why not just use the mesh? Meshes can be messy. As shown in the photogrammetry section, a mesh generated by this process typically has its texture which bears little resemblance to the resulting mesh. Thus is it necessary to retopologize and rebake the texture. By retopologizing the mesh, the mesh veracities are averaged together to give a much lower resolution mesh, but which contains the most important data. This allows a substantial reduction in the number of vertacies which in turn reduces the amount of computing power is required to work with the meshes themselves. After the new mesh is created, the image must be baked (rendered) onto the new surface. This allows for the image to be wrapped in a way that is much more legible to us. The resulting image texture to the right shows the increased legibility of this process. This method allows for the retention of data with more fidelity than a typical 2d texture. This complexity allows for a more direct representation of a given physical material yet also allows for a computationally light render. By using this method, I was able to recreate a large model with a material and textural fidelity of an actual physical model. Yet still able to use the model in the creation of various forms of architectural representation.
![]()
Why “fake” a texture? The information is all there. By using a mesh to generate 2d data, we are truncating the data generated during the photogrammetry process. Why not just use the mesh? Meshes can be messy. As shown in the photogrammetry section, a mesh generated by this process typically has its texture which bears little resemblance to the resulting mesh. Thus is it necessary to retopologize and rebake the texture. By retopologizing the mesh, the mesh veracities are averaged together to give a much lower resolution mesh, but which contains the most important data. This allows a substantial reduction in the number of vertacies which in turn reduces the amount of computing power is required to work with the meshes themselves. After the new mesh is created, the image must be baked (rendered) onto the new surface. This allows for the image to be wrapped in a way that is much more legible to us. The resulting image texture to the right shows the increased legibility of this process. This method allows for the retention of data with more fidelity than a typical 2d texture. This complexity allows for a more direct representation of a given physical material yet also allows for a computationally light render. By using this method, I was able to recreate a large model with a material and textural fidelity of an actual physical model. Yet still able to use the model in the creation of various forms of architectural representation.

